FONTANA R.D.

EXPERTISE AND INNOVATION IN FASTENED JOINTS
R&D is the fulcrum of Fontana Group’s excellence: it is fed and built daily through constantly searching for innovative solutions for customer-fastening systems.
The company Fontana R.D. – Research and Development – therefore, within the Group, is a partner for designers during innovative solutions’ design and development phases.
Research on a simple piece such as a screw or bolt implies a considerable amount of studies, experiments, and field tests: we work to create fasteners based on a specific customer design. We start by defining the needs and performing dynamic simulation tests to arrive at the production of the pieces according to the required mechanical and quantitative requirements. We develop optimal solutions for product use, identifying the most suitable solution for each assembly and fastening requirement.
RESEARCH & DEVELOPMENT

WHERE
R&D is the fulcrum of Fontana Group’s excellence, where ideas and production meet and coordinate by the EMEA R&D CENTER of Veduggio con Colzano. There are also two centers in Fenton (Michigan) and Atibaia (Brazil) offices.
WHO
The Fontana R.D. team comprises professionals with extensive experience in metallurgy, mechanics, measurements, and sensors. Furthermore, to guarantee the correct and optimal use of the fasteners for the various applications, the Group is present near the customer’s plants with its application engineers, who ensure the system’s integrity even in the production phase. All to maximize performance, increase quality, and reduce costs. The results generated then converge in case histories and technical insights, and intense training activity for experts in the sector.
WHERE
R&D is the fulcrum of Fontana Group’s excellence, where ideas and production meet and coordinate by the EMEA R&D CENTER of Veduggio con Colzano. There are also two centers in Fenton (Michigan) and Atibaia (Brazil) offices.
WHO
The Fontana R.D. team comprises professionals with extensive experience in metallurgy, mechanics, measurements, and sensors. Furthermore, to guarantee the correct and optimal use of the fasteners for the various applications, the Group is present near the customer’s plants with its application engineers, who ensure the system’s integrity even in the production phase. All to maximize performance, increase quality, and reduce costs. The results generated then converge in case histories and technical insights, and intense training activity for experts in the sector.
WHAT
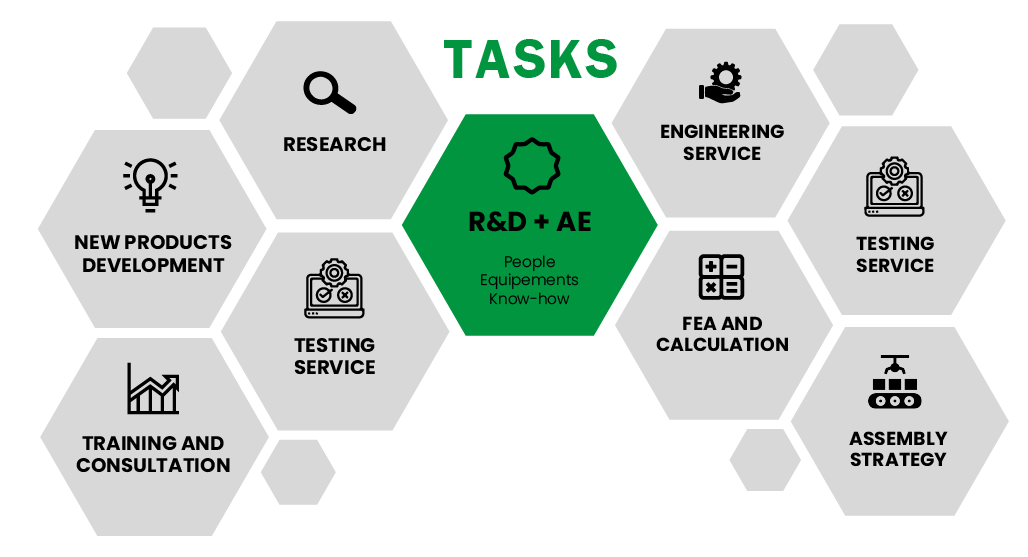
Testing capability:
• Torque/Tension test at bench (RT and warm)
• Torque/Tension test on assembly (ultrasonic, strain-gages)
• Loosening tests at bench (temperature, vibration, bending)
• Loosening tests on field (track test on vehicles)
• Telemetry
• Fatigue test (standard, warm, eccentric)
• Corrosion test (salt spray, CASS, cyclic, climatic, acid/alkaline aggression)
• Mechanical test
• Metallurgy
• Hydrogen embrittlement test
• Cleanliness test
Design capability:
• Bolt design (load calculation)
• Joint design (FEA on assembly)
WHAT
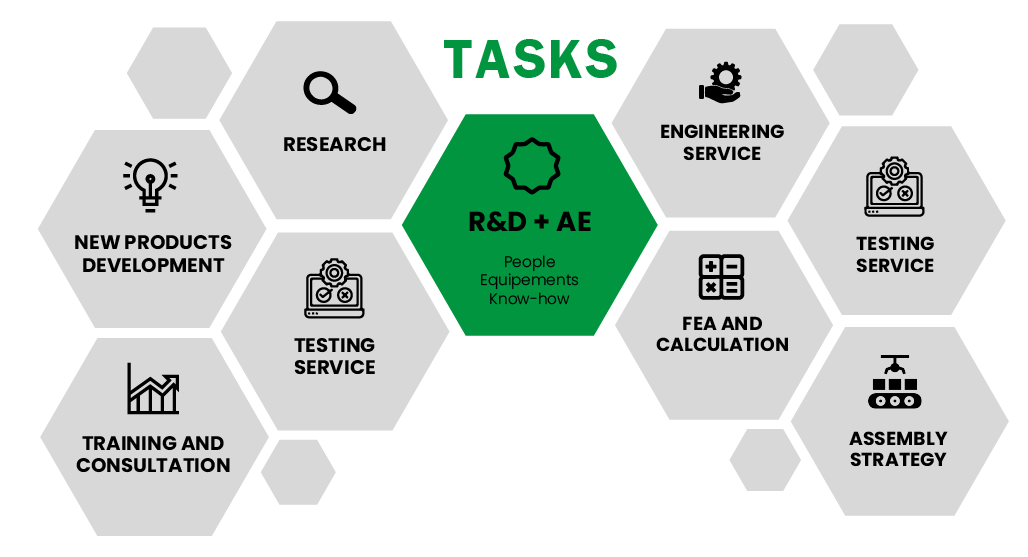